Steven Jarman’s Joinery Journey – embracing challenges to craft exceptional joinery
Thursday, November 28th 2024
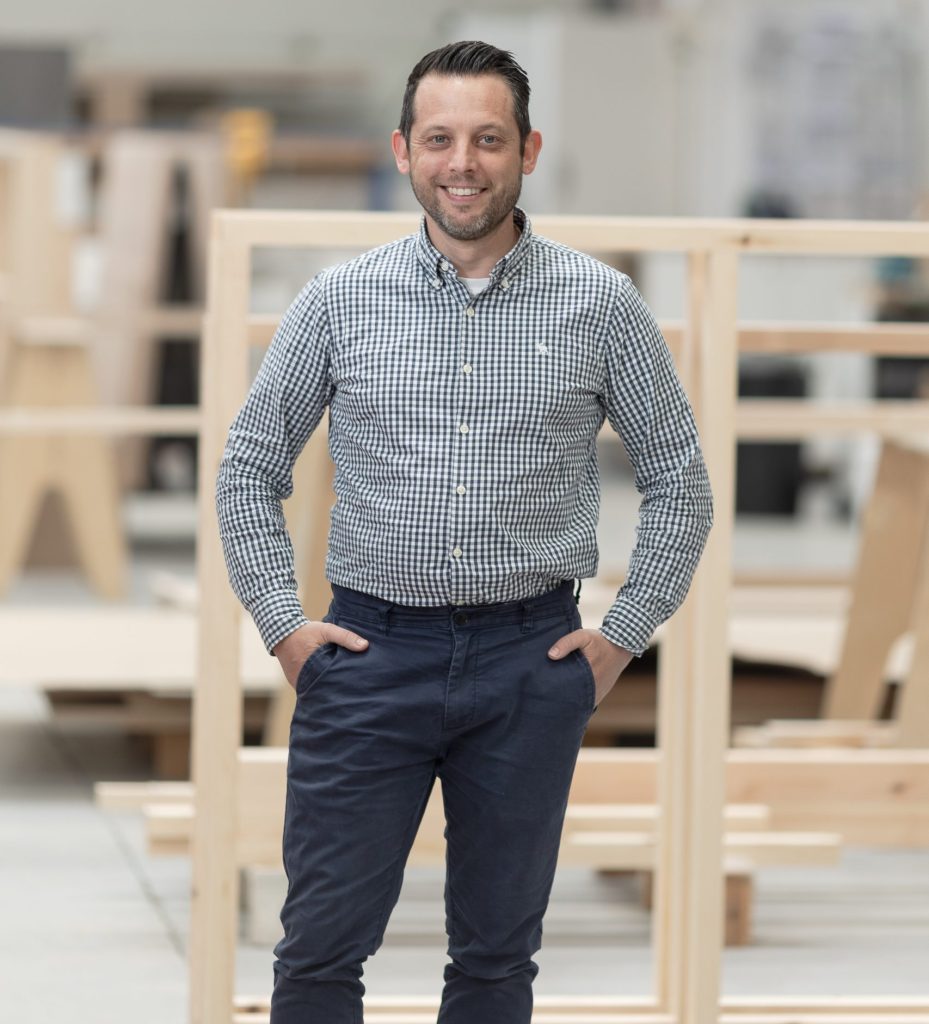
Tell us about your journey in the industry. How did you get started?
My journey into joinery has been fairly short, as I’ve only been working at Denne Joinery for a year and a half. Before that, I spent 28 years in the fitted furniture industry. After managing a large project, I needed a new challenge. Denne, being leaders in the joinery industry, felt like the right place to start, as I wanted to explore the commercial joinery world. It was certainly the right choice! It’s been a fascinating year and a half, full of interesting projects and opportunities to further develop my skills.
Can you share a pivotal moment in your career that shaped your approach to managing joinery projects?
My last project at my previous company was a large furniture fit-out across eight floors, including a private wing of a London hospital. However, they didn’t have any other interesting projects on the horizon after this, whereas Denne Joinery was taking on more compelling jobs to create bespoke joinery with different designs for various customers. I wanted to keep moving forward and to progress.
It is the bespoke nature of what we do at Denne Joinery that makes every job different. Every joinery project is a challenge, but the end product is always exceptional. It’s very rewarding. Denne Joinery has perfected its process, and everything is very well run. The Denne Way is key to tackling large projects, and I would imagine there are lots of companies out there striving to follow their lead. The ISO9001 and 1401 are accreditations that prove all the work that goes on behind the scenes.
Denne Joinery has a system in place and an exceptional team, so projects are managed very professionally and to a high standard. Project Managers have got the support of the whole team at all times. I can lean on my colleagues, and we work together on creative ideas to deliver the highest quality craftsmanship.
What are you most passionate about in your role?
I love seeing the end results. There is a lot of dedication going into each product all through design stage, when the pieces of joinery are envisioned, to the manufacturing and installation. It’s also incredibly inspiring to get a very satisfied customer with the transformation of their space once our bespoke joinery is in place. We deliver high-quality joinery and it’s something to be proud of. The whole team at Denne Joinery has a deep-rooted passion for joinery and I can see why.
What are the biggest challenges you face in terms of project management on-site?
Normally, the challenge is timing. It’s very fast-paced from day one and we often need to take full ownership to ensure that everyone is doing their part to keep the project on track. Our customers trust us to coordinate all trades and hand over on time. It is also important to hit the milestones set, so we can share updates with our customers. We bring them onto the journey, making them feel connected to the project as it moves forward.
What key factors do you consider when planning the timeline for a joinery project?
Denne Joinery is very good at managing every step of the project. As soon as we receive an order, we produce a programme that outlines exactly what is required from each person involved and from the customer, ensuring we deliver by the set critical dates. For instance, I work closely with the design team, and we all know it is essential to send the designs to manufacturing to meet the deadline. The whole team works together towards that goal.
What sets Denne Joinery apart when it comes to project planning?
We take the customer through the whole joinery journey. When we receive the key information, architectural drawings and a scope, we take the customer’s vision and produce our drawings to craft the bespoke joinery that will ultimately make up the exceptional interior they had envisioned. Our design process, sampling and workshop tours and the way we manage the project sets us apart. It’s the Denne Way. When customers come to our world-class manufacturing facilities, it helps them understand all the work that goes into producing high-quality, bespoke joinery. It promotes transparency and confidence.
How do you manage quality control throughout the joinery production and installation phases?
During joinery production, I like visiting the workshop once a week to see the joinery coming through and personally doing a bit of quality control myself. On site, my team of site managers and I do thorough checks when the joinery arrives. We have a snagging sheet to take notes. If an item needs tweaking, we revisit it and, if needed, we communicate back to the workshop to make sure it complies with the highest standards.
CNC machines play a very important role in minimising snags from the outset. I used to operate CNC machines years ago and I know very well how important their role is. At Denne Joinery, we always footprint templates first to make sure everything is up to standard, especially when crafting very bespoke joinery. These templates give you not only the footprint of that particular joinery rod, but they also outline where we need to bring services up. Then, we lay that template down and we check it with other trades, such as electricians and plumbers. We take it to the floor and we work with it to ensure that everything is in the right place. Denne Joinery is at the forefront of the industry. We don’t have to do all of that, but we do it to minimise snags and make installation easier, avoiding delays as well.
What role does sustainability play in your project management, especially in terms of materials and waste management?
Sustainability is very present from the outset of each project, understanding what is expected of us. We give our customers an understanding of products and finishes because they have an impact on the ESG standards they want to meet. It is essential to know what the environmental requirements are when sourcing compliant products.
One of the latest projects that I’ve worked on where sustainability was paramount was Sumitomo. It was a very interesting project, as we had to collaborate with their own sustainability consultant.
Denne Joinery stands out in the industry, as we’re striving to bring the ESG framework to the centre of all our projects. Our credentials give our partners confidence that we are dedicated to ensuring consistently high standards, and accreditations such as BREEAM, SKA and FSC are becoming more and more central.