A rare talent: Veneering with Michael Twyman
Monday, 24th February 2025
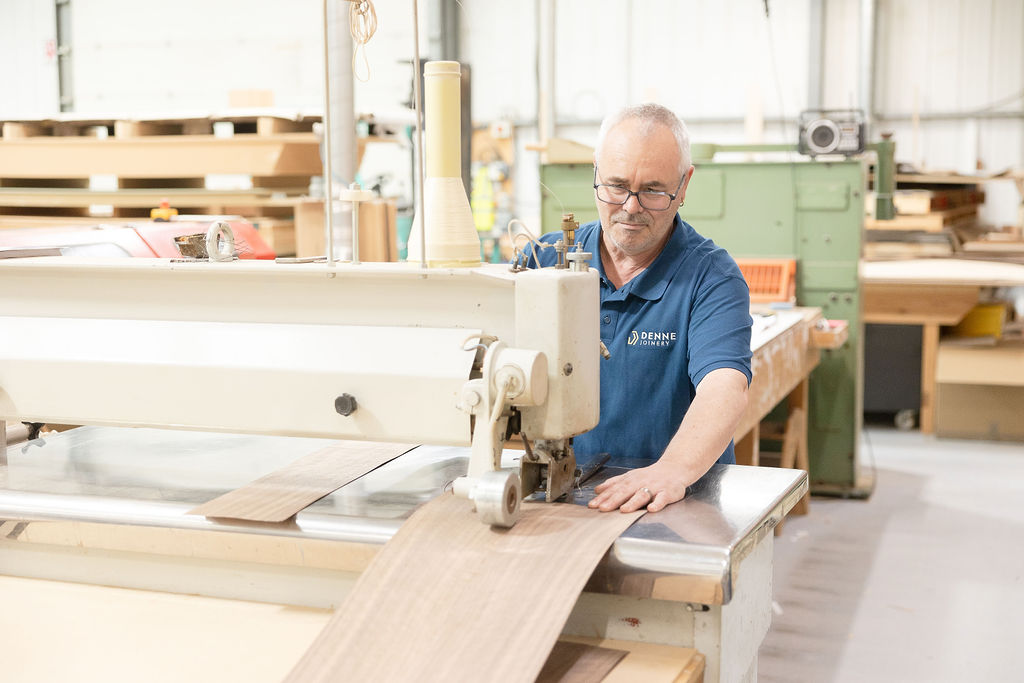
Michael Twyman is a veneerer with more than 40 years of experience. His unique skill set makes him a true industry expert, as veneering remains rare and highly specialised in the UK.
Veneering involves applying a thin layer of quality wood (veneer) onto a piece of joinery. This technique allows us to achieve the look of solid timber with less material, improving sustainability and design flexibility. Our in-house veneering department plays a crucial role in delivering the highest quality finishes to our bespoke joinery projects.
Today, we explore Michael’s journey into becoming one of the country’s rare expert veneerers and the dedication it takes to master this exceptional trade.
Could you tell us a bit about your journey in the industry? How did you get started?
My joinery journey started when I was 18 years old. At the time, the company used a piecework model, which meant that we got paid for what we did. After a couple of weeks in the job, I was assigned a mentor who showed me the basics of how to operate the veneering press, including fundamental aspects like setting sizes. Back in the day, technical drawings weren’t commonly used. We mostly worked with set sizes instead. Veneering relied heavily on experience, craftsmanship and visual judgment rather than predefined design specifications.
For my first job, I created 40 sets of veneering side boards with inlay tops made of yew tree, which is a type of veneer that is quite hard to use because it has a wild, swirling grain with frequent knots and it’s prone to splitting. Throughout my first 15 years as a veneering expert, I perfected my technique as I worked on different projects. We used mostly cherry, mahogany and yew tree veneers.
One day, my mentor phoned me up to tell me about a job vacancy at another joinery workshop. In this new role, I learned to read technical drawings, a skill that became essential in my career. Not long after, I was offered a position at Denne Joinery, where I’ve continued to grow and refine my expertise. At the time, the company was expanding its world-class facilities and investing in cutting-edge machinery. It was a great opportunity to join them in their ambitious and exciting project. Together, we’ve elevated our veneering service, which is a truly unique offering that not many other joinery workshops provide.
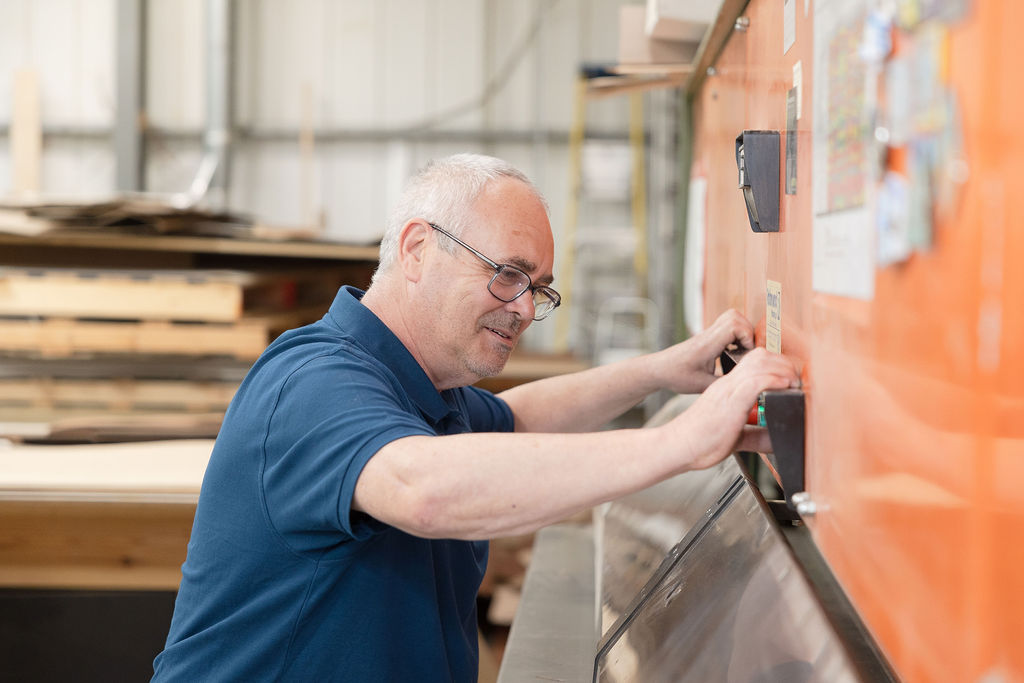
Are there any traditional techniques you still use, or has technology significantly changed veneering methods?
I still use veneer tape to join veneer sheets when they cannot be stitched. For transparent materials or lightly coloured veneer, the zig-zag glue line would be visible if using the stitching machine, so I prefer to manually tape the sheets together.
That’s probably the only old-school technique that I rely on when creating commercial joinery – everything else is done using our state-of-the-art machinery. For bespoke joinery, traditional techniques can sometimes be the best approach, especially when working with one-of-a-kind pieces that require precision and craftsmanship.
After 25 years on the team, every day still presents opportunities to learn as technology evolves. Recently, we developed a new internal process to veneer a specific type of engineered panels. After de-taping the panels, they need to be put through the sander and then sanded manually on the bench. They can then be sent to the finishing studio. If we don’t follow this process, the tape marks will remain visible even after applying the finishes.
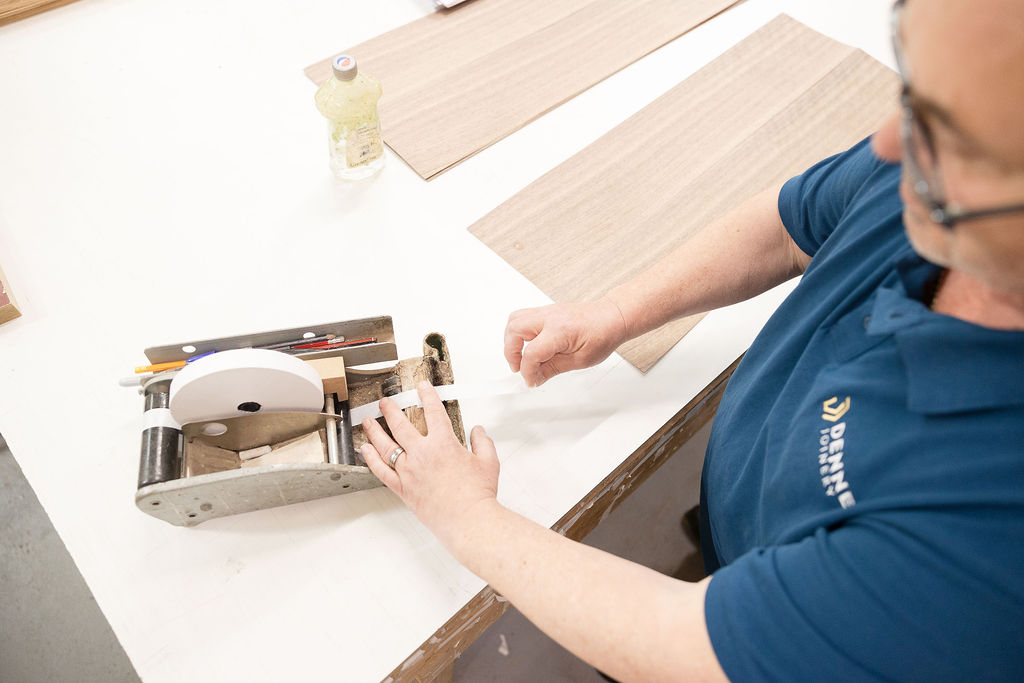
Have you got any preferred materials to work with for veneers, and why?
Personally, I like American black walnut. It’s a versatile material that strikes the perfect balance—easy to work with yet naturally resilient. Its rich tones and fine grain also give it a timeless, elegant look.
What are you most passionate about in your role?
I’m passionate about quality – I like things to be done right. I take pride in my attention to detail and strive to pass that knowledge on to colleagues and apprentices, ensuring that high standards are maintained across every project.
Seeing the progress of people in the workshop is also incredibly rewarding. Watching apprentices and team members develop their skills and grow in confidence makes the job even more fulfilling.
What advice would you give to someone new to veneering who wants to master the craft?
First and foremost, measure carefully – precision is key to ensuring the right fit. Selecting the right veneer would be the second most important thing. And, lastly, always aim for the highest quality, paying attention to the smallest details. Take pride in your work. Veneering is an art, and mastering it comes from dedication, patience and a commitment to excellence.
Get in touch to start your joinery joinery with us.